Special casting technology Vacuum die-casting
Vacuum die-casting is a technology used for the purpose of reducing the gas content in the product, which is a shortcoming of die-casting, and to improve the flow of the molten metal by reducing the pressure in the cavity with the use of a vacuum tank in advance before pouring the molten metal.
By employing our independently designed MSV (sensor-type vacuum), it is possible to decompress immediately before completing the pouring process, which enables high-vacuum die-casting to be performed.
*MSV is a system that works by having sensors installed in the cavity; when the molten metal reaches these sensors, the vacuum valve automatically shuts off.
Local pressurized die-casting
Local pressurized die-casting is a die-casting method whereby, after molten metal is poured into the mold cavity, pins are used to pressurize parts of the cavity prior to solidification in order to obtain a product with less porosity.
Setting pressurizing points near thick-walled parts of the product is primarily done to inhibit the occurrence of shrinkage cavities. Since solidification occurs quickly, however, the timing of pressurization is vitally important.
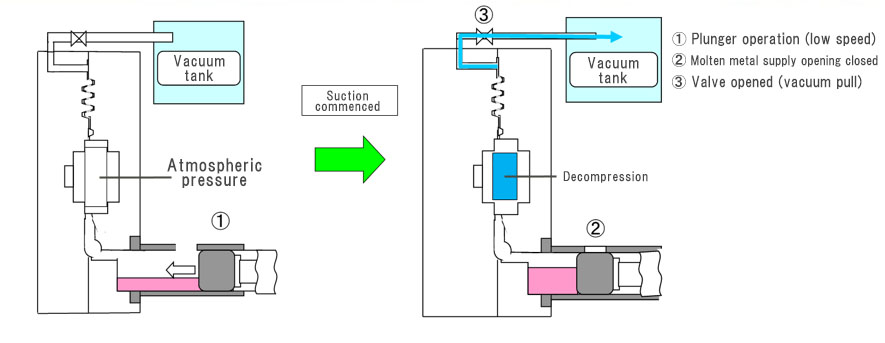
Pulse spraying
Pulse spraying is carried out by controlling intermittent application with the nozzle of the spraying device.
When spraying the release agent, a normal spray sprays the liquid release agent during operation on a constant basis. In contrast, a pulse spray allows the release agent to be applied efficiently by opening and closing the spray nozzle in rapid succession to repeat the cycle of spraying and stopping at short intervals of around 1 to 5 milliseconds per cycle. The amount of release agent that is consumed is less than is consumed with a conventional approach. Pulse spraying is also more environmentally friendly.
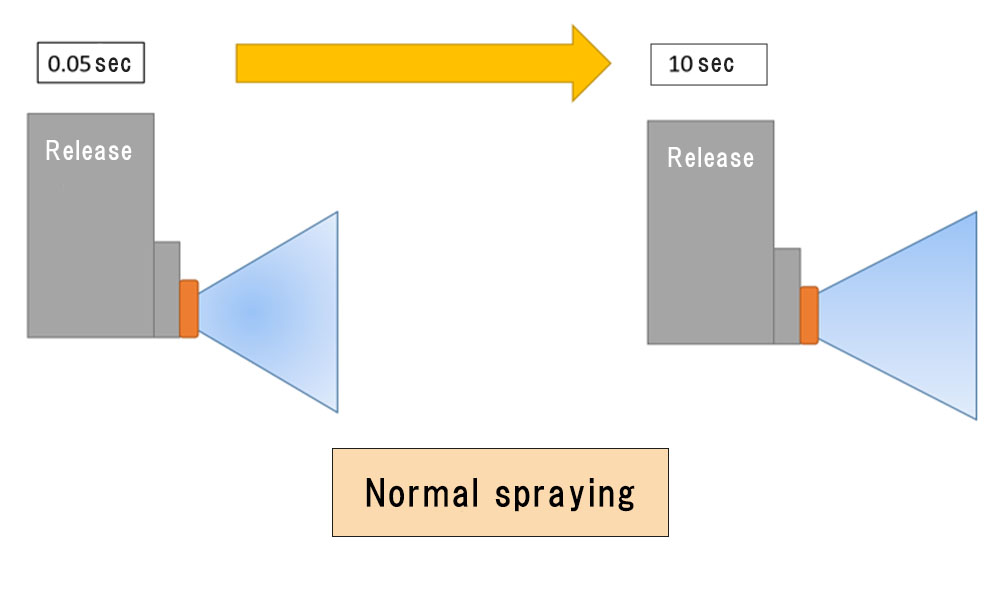
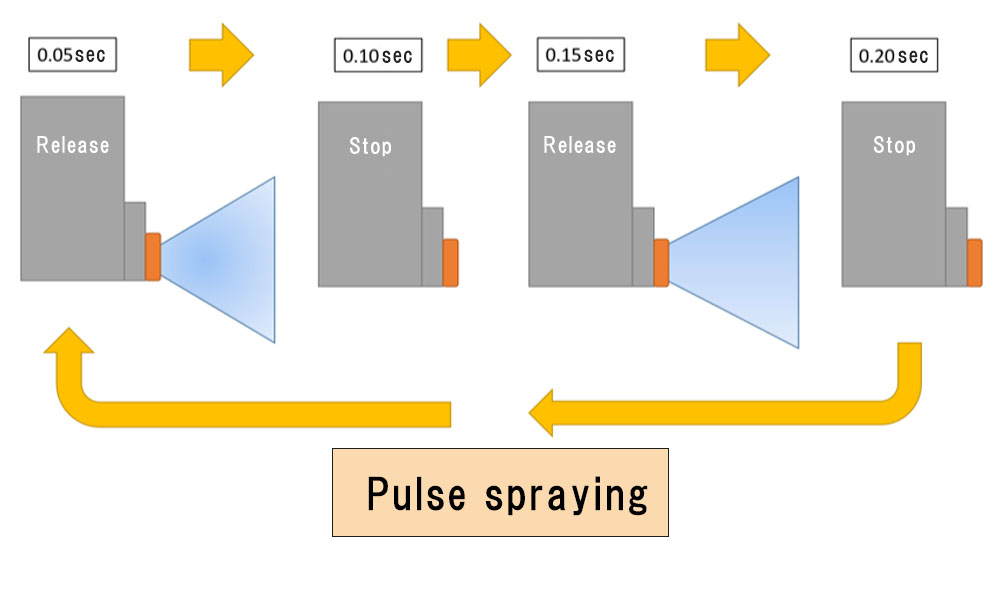
A slide structure refers to a structure that is used when forming an undercut shape. An undercut shape is a shape that cannot be removed with normal mold movements.
In order to form an undercut shape, a mechanism that can be moved with the use of tilted pins or cylinders is built into the mold.
This permits various shapes to be formed and more needs to be met. By using a pincer structure or multi-tiered cylinders and cylinders of a smaller diameter than usual, we also contribute to carbon neutrality through high cycle times and energy-saving results.
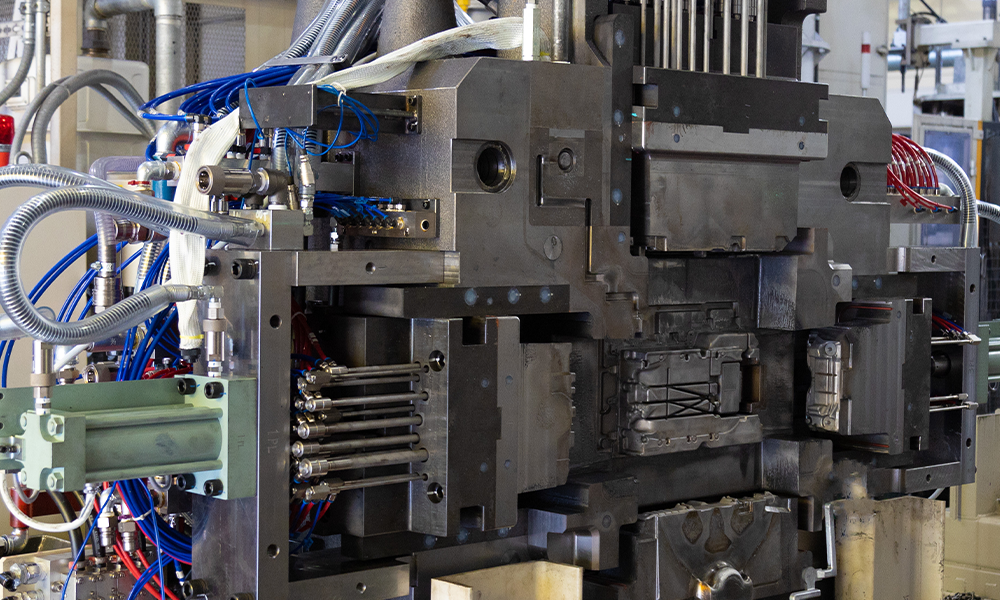