Downsizing
When it comes to die-casting, force that could cause the mold to open is exerted when metal is cast in a mold at high speed and high pressure.
To prevent the mold from opening at this time, a larger casting machine is needed. However, we have been working to downsize in a way that allows us to cast with smaller casting machines than usual. While a die-casting machine rated at 2,000 tons or more is normally used for complex products to be cast with around 80 MPa of pressure exerted, we cast with a 1,100-ton-class die-casting machine that has been designed to ensure quality with even 40 MPa of pressure exerted.
This provides us with numerous advantages, including a lower cost per product produced due to the smaller size of facilities used and an ability to contribute to carbon neutrality through a reduction in the amount of fuel used for operating our facilities.
On the other hand, we are forced to cast at a lower speed and lower pressure than normal, which makes the ensuring of quality an issue. Nevertheless, this issue has been resolved through the implementation of the PDCA cycle at the design and prototyping stages based on the use of casting analysis and various types of evaluation facilities.
Evaluation facilities for downsizing
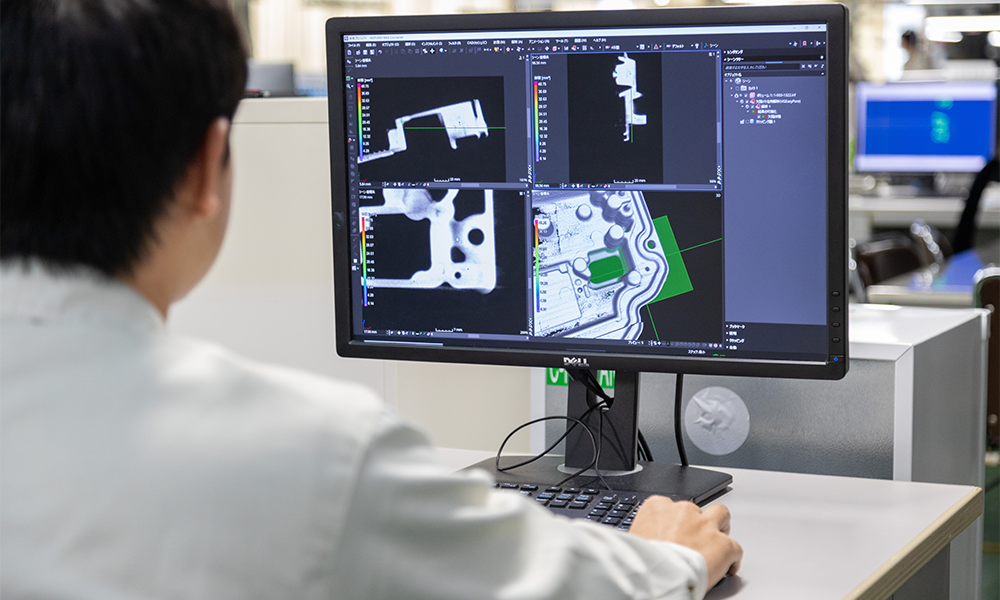
CT scanner
A CT scanner uses X-rays, which are also utilized in X-ray and MRI systems found in healthcare settings and allows you to peek inside products that would normally have to be cut open or otherwise destroyed to be evaluated.
It is primarily used to evaluate porosity inside products and check the internal quality of, for example, parts that need to be airtight as a way of working on achieving various quality improvements.
Gas quantity-measuring instrument
Since the manufacturing process known as die-casting uses lubricants and water, these substances become trapped in the product at the time it is formed. When exerting an external force to cast high-temperature molten metal into a mold at high speed, evaporation occurs to cause gases to remain inside the product and casting defects to result.
By measuring the amount of gases contained in a die-cast product with a gas quantity-measuring instrument, the results are used to optimize the casting conditions.
SEM / EDX
A scanning electron microscope (SEM) is a device that can capture images of objects magnified by up to a million times and allows users to see irregularities and aspects of the surface of a product that cannot be discerned with the naked eye. By enabling defects to be visually examined at their surface, this device can be used to narrow down the potential causes of their occurrence.
Just like an SEM, an energy dispersive X-ray analysis (EDX) device uses electron beams to detect special X-rays and to identify the atoms that comprise a given substance through elemental analysis. It can also be used to identify foreign particles in a product and to help improve the quality of molten metal.
Microscope
A microscope is an instrument used to magnify objects with a camera. Since the scope part can be moved freely without having to stay in close contact with the object being observed, a microscope can be used on various products, including the nooks and crannies of products with large irregularities.
By visually examining a polished product, you can check the metallographic structure. A microscope can be used to assess the internal quality of a product based on its structural aspects and to analyze the causes of defects in the product.