The flow of steps until the product is finished
The casting process comprises several steps. At MINO, it is characterized by a high degree of flexibility and the use of downsized facilities.
Trimming process
The product part and casting plan part (part through which aluminum flows), which are characteristic elements of die-casting, are separated from one another. The trimming process provides the flexibility to accommodate a wide range of plans.
Cooling process
Products removed at high temperatures are cooled down in specialized facilities and stabilized within a safe range of temperatures.
Finishing process
●●Finishing by robots
Robot-mounted blades are used to remove casting burrs that could not be removed through the trimming process.
●Shot blasting
The entire product is blasted with fine metallic particles to remove fine burrs (characterized by a high degree of versatility).
Correction process
Die-cast products that have become deformed through the solidification and shrinkage process are corrected and stabilized with the use of our proprietary straightening machine.
Automatic lines
We are working on lines to automate the trimming process (process of removing the unnecessary parts of products) and finishing process (process of removing casting burrs) through the use of different kinds of robots designed to perform work that used to be manually done.
We aim to harness automation to achieve high levels of productivity and stabilize quality. We also hope that automation will help create plants that are environmentally and people-friendly by rendering processes more environmentally friendly (by way of limiting noise generation and saving energy) and reducing the physical load on employees based on the four principles of motion economy.
Unmanned lines
We are also working to streamline the flow of people and objects by proactively introducing automatic guided vehicles (AGVs), which have substantially evolved in recent years. The advantages of AGVs include the following: reduces the number of transport workers (reduces labor costs), accurately moves products to the right lines (prevents conveyance mistakes), and conveys products at predetermined times (for improved productivity). In addition, IoT monitoring technology that we have developed in-house is used to enable the high-precision detection of defects by robots in order to accommodate the accelerating pace of digital transformation (DX) in industrial settings.
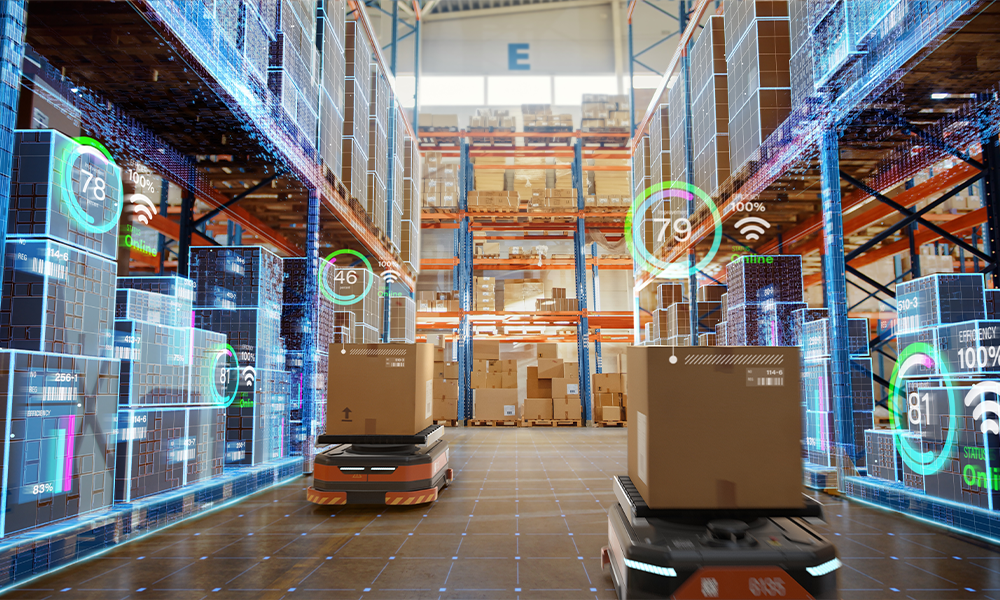