Thin-walled forms
We produce products with walls that are 0.8 millimeters thick and that conform to a sack-type structure. These products are built into various automobiles to help improve fuel efficiency.
In addition, we received the Urakami Prize as conferred by the Japan Die Casting Association for these products in 2006. We also succeeded in casting a die-cast prototype with walls that are 0.45 millimeters thick, which is thinner than the lead used in a mechanical pencil. For this particular prototype, we were awarded the Technology Prize as conferred by the Japan Aluminium Association in 2008.
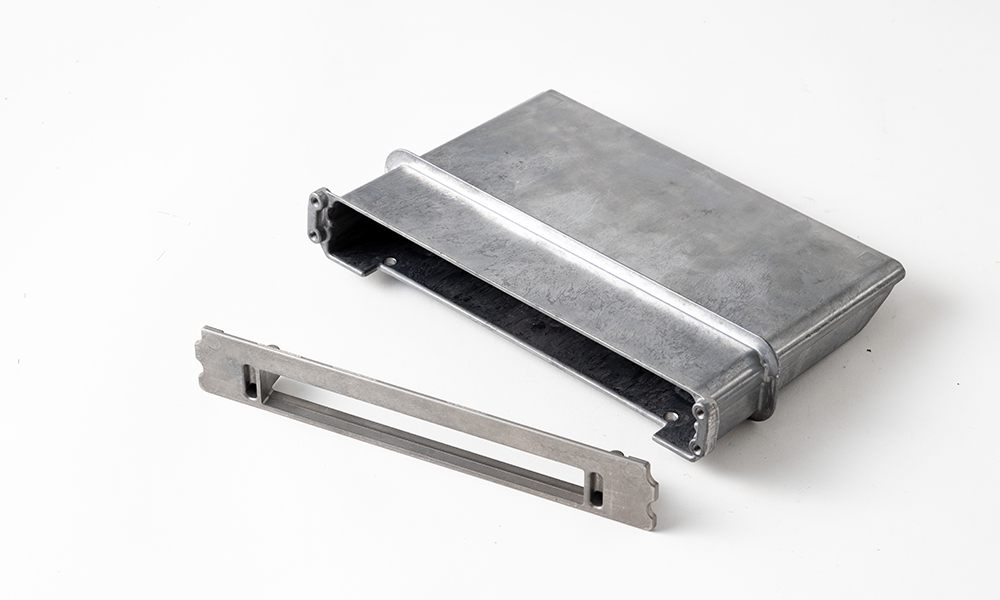
Complex forms
We produce complex, large products with multiple sliding features on the top, bottom, left, and right sides as can be seen in converter cases. In addition, these products also need to be highly airtight, undergo leak testing with helium, and are press fit with pipes. They are designed for the electrification of automobiles, which is well on its way to becoming a mainstream feature of the industry. We expect to see many similar products become commercially available in the future.
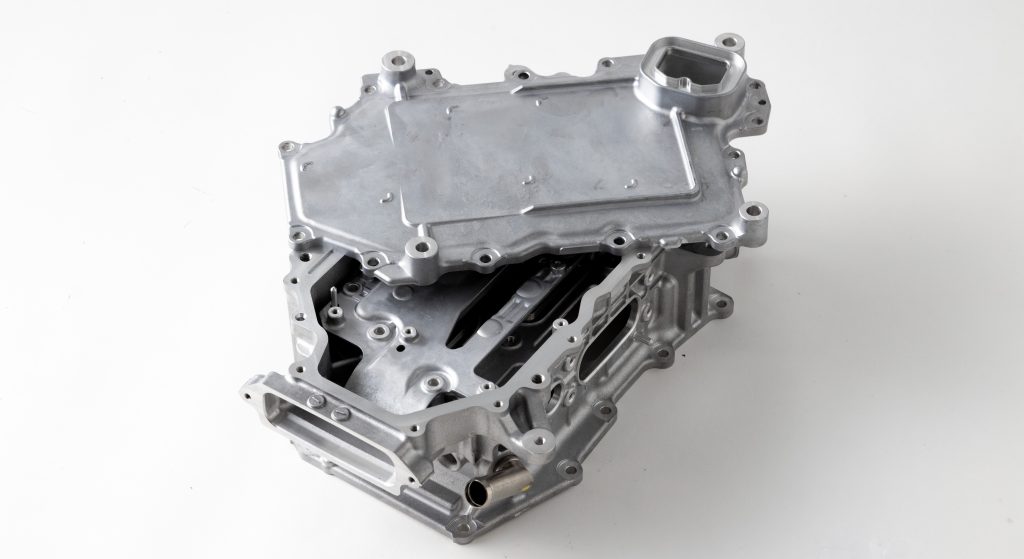
Insert casting
We perform insert casting to integrate aluminum and different material components into the same mold. By casting after inserting components into a mold, we can integrate different materials and help reduce the number of parts used to manufacture automobiles. Precision used to be achieved by additional processing after integral molding was undertaken. However, we were able to achieve dimensional precision with just die-casting alone so as to eliminate this sort of processing. By automating the insert casting process with robots, we established a system for producing at least 2 million units a year.
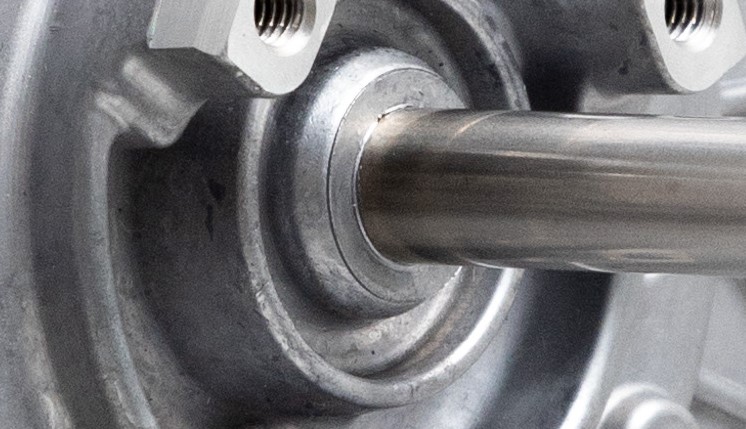
Compatible with a wide range of different materials
A typical material used with die-casting is ADC12, but we also produce castings made with other materials. Since the properties of materials vary, the technology needed to produce high-quality products differs. Nevertheless, we have cast with materials that are closer to pure aluminum, have accumulated know-how with respect to changing the materials with which molds are made, and are able to provide solutions that meet the needs of our clients.
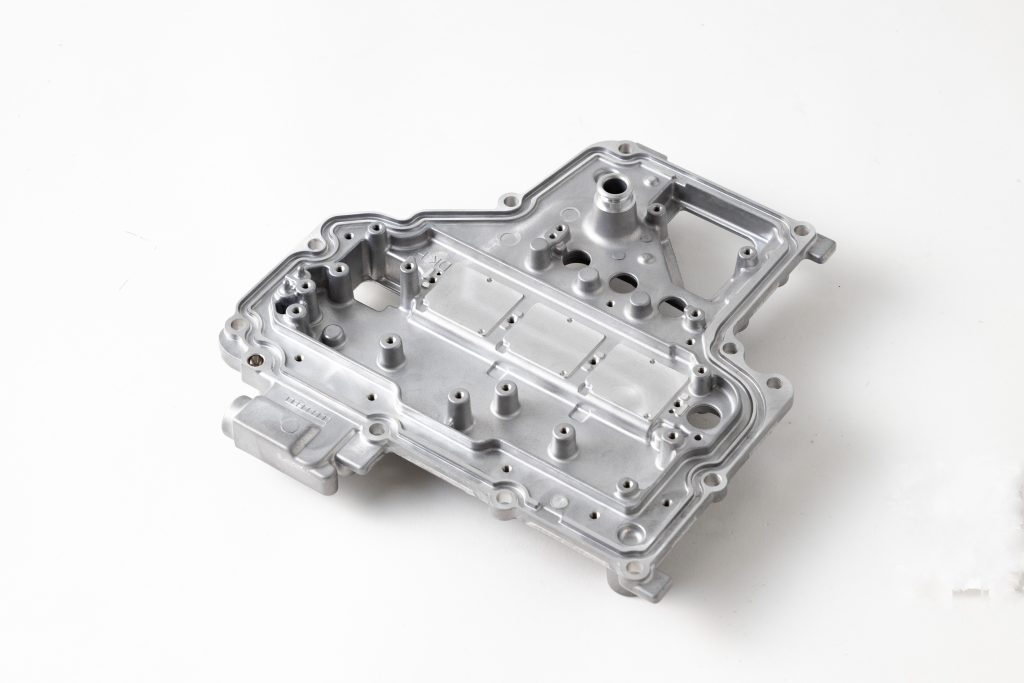